Video
General description
TP-TGXG-200 Automatic Bottle Capping Machine is used to screw caps on bottles automatically. It is widely applied in food, pharmaceuticals, chemical industries and so on. There is no limit on shape, material, size of normal bottles and screw caps. The continuous capping type makes TP-TGXG-200 adapt to various packing line speed. This machine really has multiple purposes, which is applied widely and easy-operating. Comparing with traditional intermittent working type, TP-TGXG-200 is more high-efficiency, tighter pressing, and cause less harm to caps.
Application
The automatic capping machine can be used on bottles with screw caps in various sizes, shapes as well materials.
A. Bottle size
It is suitable for bottles with 20-120mm diameter and 60-180mm height. But it can be customized on suitable bottle size beyond this range as well.
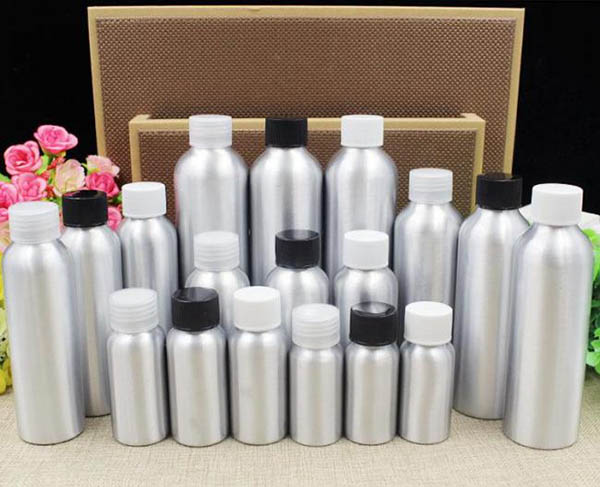
B. Bottle shape
The automatic capping machine can be applied on various shapes like round square or complicated shape.
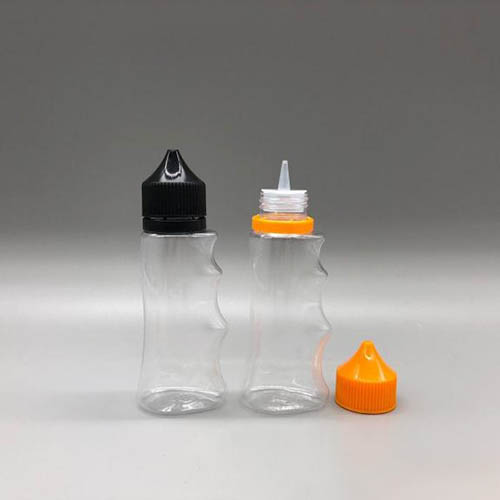
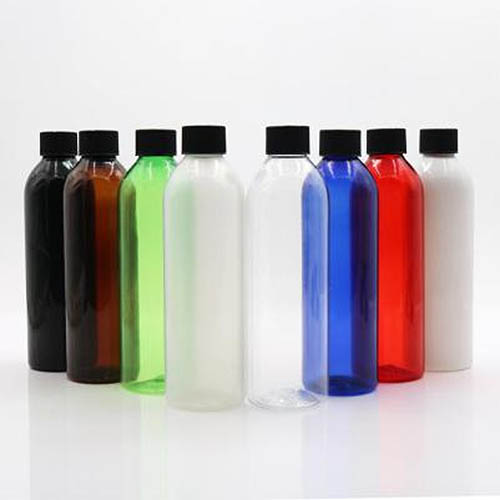
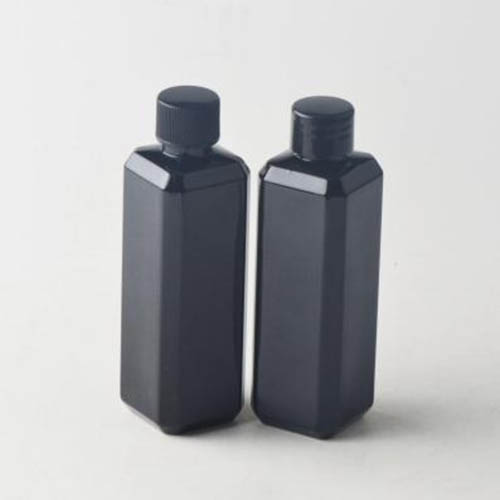
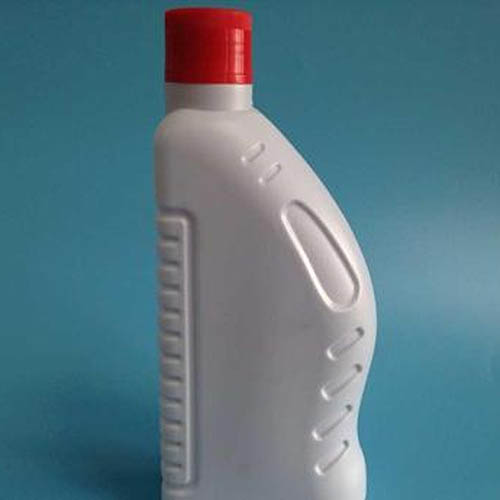
C. Bottle and cap material
Whatever the glass plastic or metal, the automatic capping machine can handle all of them.
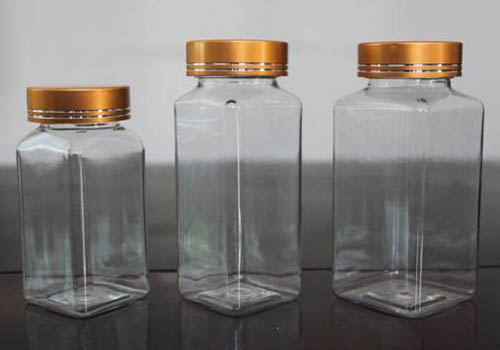
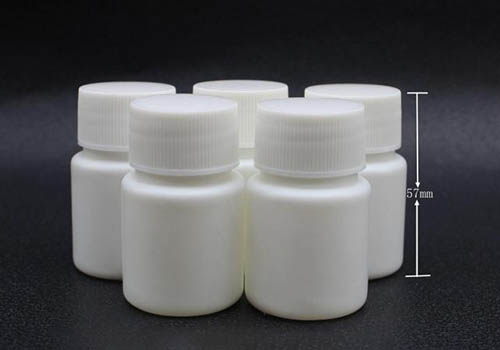
D. Screw cap type
The automatic capping machine can screw all kinds of screw cap, like pump, spray, drop cap and so on.
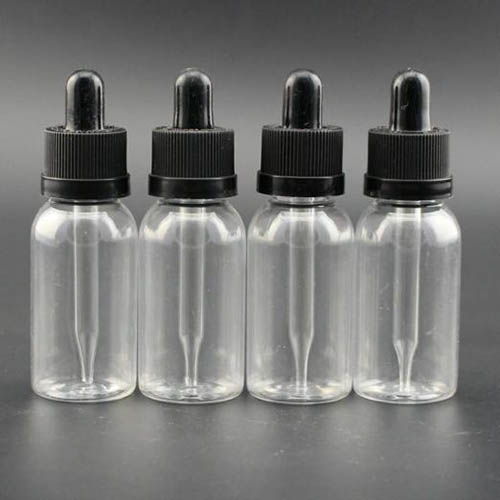
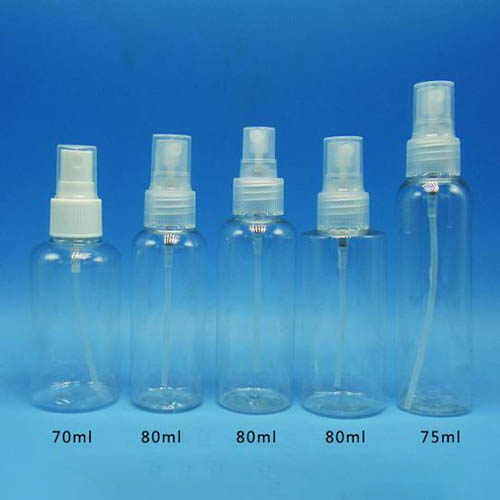
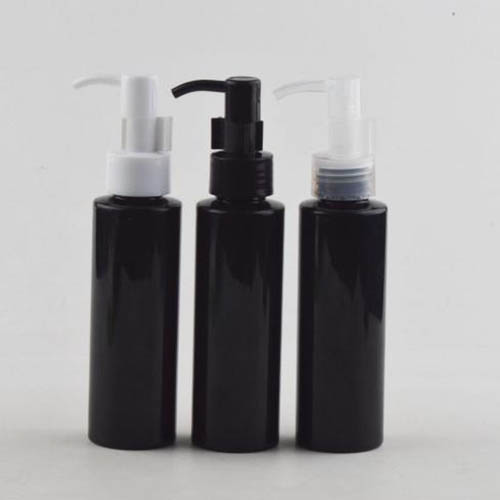
E. Industry
The automatic capping machine can join all kinds of industries no matter it is the powder, liquid, granule packing line, or it is the food, medicine, chemistry or any other industry. Wherever there is screw caps, there is automatic capping machine to work with.
Construction & working process
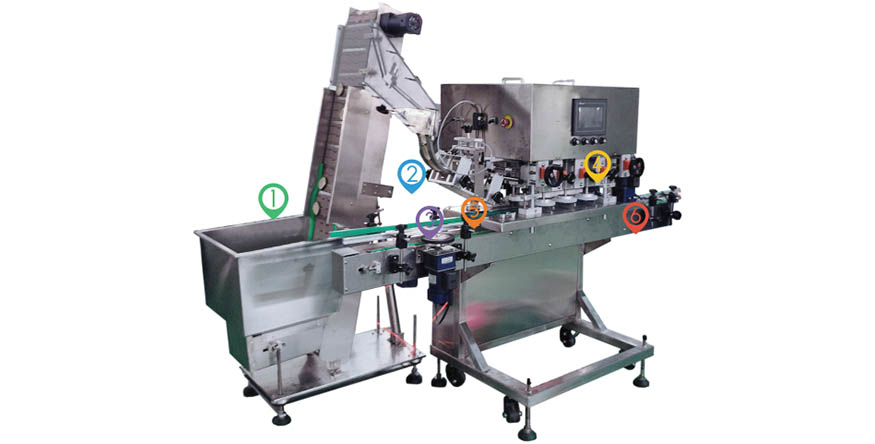
It consists of capping machine and cap feeder.
1. Cap feeder
2. Cap placing
3. Bottle separator
4. Capping wheels
5. Bottle clamping belt
6. Bottle conveying belt
Followings are working process
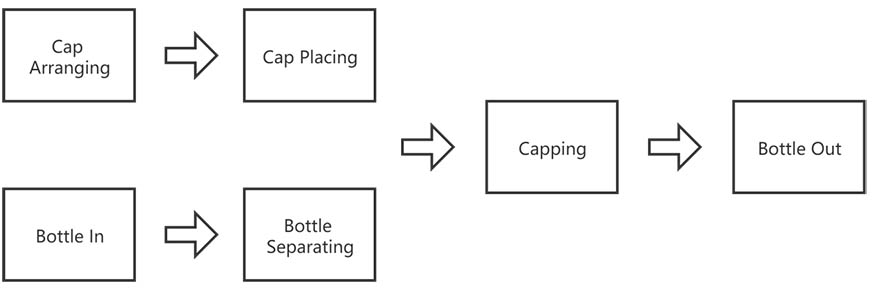
Features
■ Widely used in bottles and caps of various shapes and material.
■ PLC&touch screen control, easy to operate.
■ Easy operation and easy adjustment, save much more human source as well time cost.
■ High and adjustable speed, which is suitable for all kinds of packing line.
■ Stable performance and high accurate.
■ One button starting function brings about much convenience.
■ Detailed design makes the machine more humanized and intelligent.
■ Good ratio on outlook of machine, high level design and appearance.
■ Machine body is made of SUS 304, meet GMP standard.
■ All the contact parts with bottle and lids are made of material safety for food.
■ Digital display screen to show the size of different bottle, which will be convenient for changing bottle(Option).
■ Optronic sensor to remove the bottles which are error capped (Option).
■ Stepped lifting device to feed in lids automatically.
■ Lid falling part can remove error lids away(by air blowing and weight measuring).
■ The belt to press the lids is inclined, so it can adjust the lid into the correct place and then pressing.
Intelligent
Use the principle of different center balance on two sides of cap, only correct direction cap can be moved up to top. The cap in wrong direction will be fall down automatically.
After the conveyor bringing caps on top, the blower blows caps into cap track.
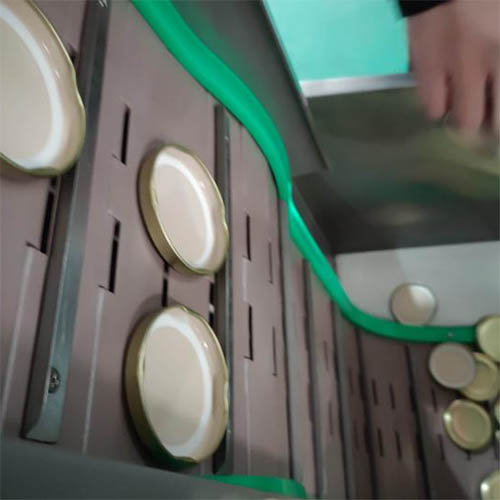
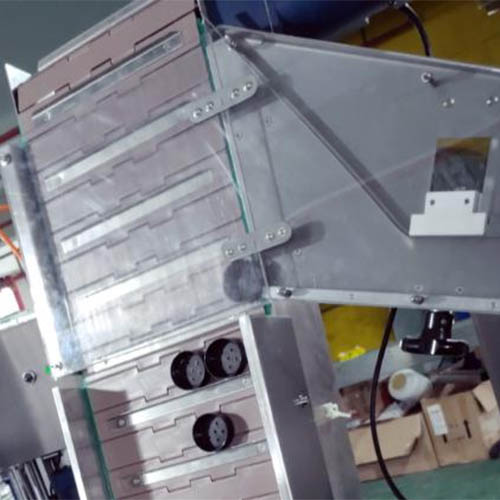
Error lids sensor can detect inverted lids easily. Automatic error caps remover and bottle sensor, reach the good capping effect
Bottle separator will separate bottles from each other by adjusting the moving speed of bottles at its position. Round bottles normally need one separator, and square bottles need two opposite separators.
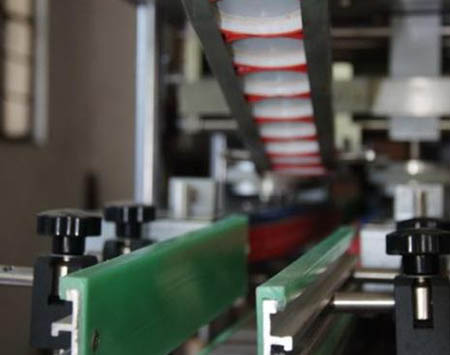
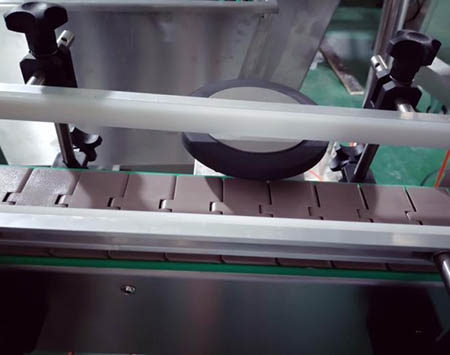
Cap lack detecting device controls cap feeder running and stopping automatically. There are two sensors at two sides of the cap track, one to check if the track is filled with caps, the other to check if the track is empty.
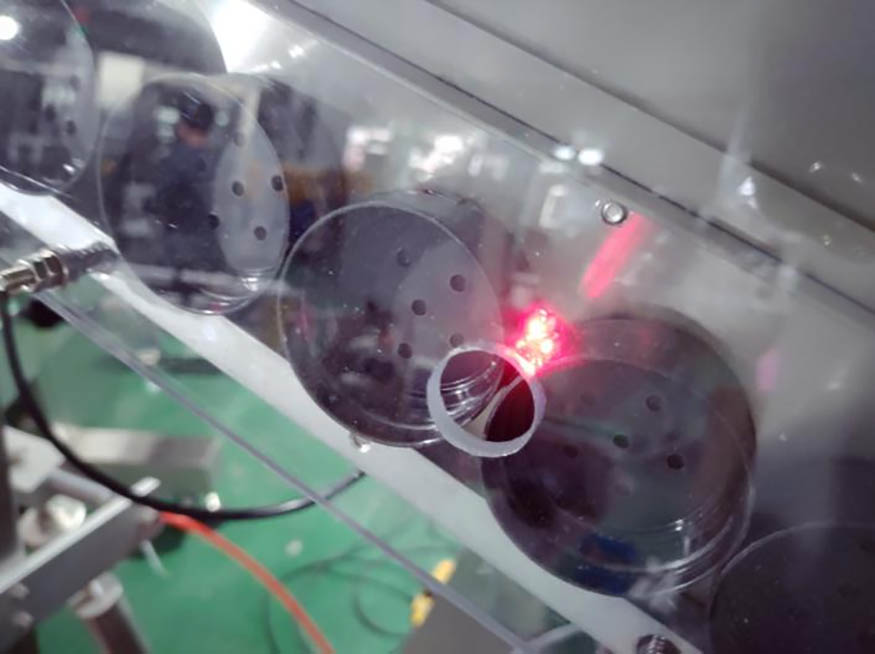
Efficient
The maximum speed of bottle conveyor and cap feeder can reach 100 bpm, which brings the machine high speed to suit various packing line.
Three pairs of wheels twist caps off fast. Each of the pair has the specific function. The first pair can turn reversely to make difficult placing caps be in its correct position. But they can make caps turning down to reach a suitable position fast together with the second pairs wheels when the cap is normal. The third pairs adjust slightly to tight the cap, so their speed is slowest among all wheels.
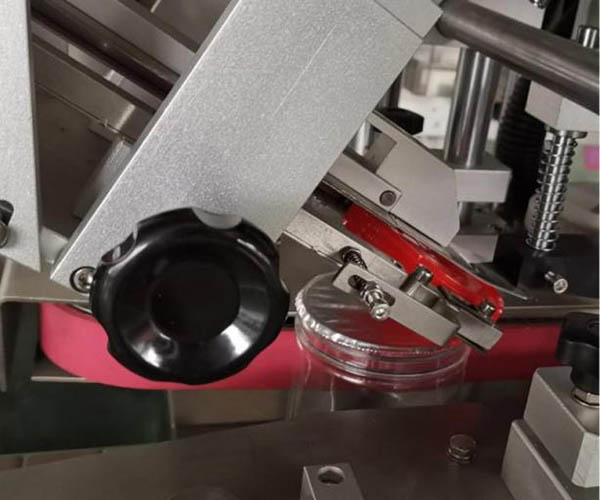
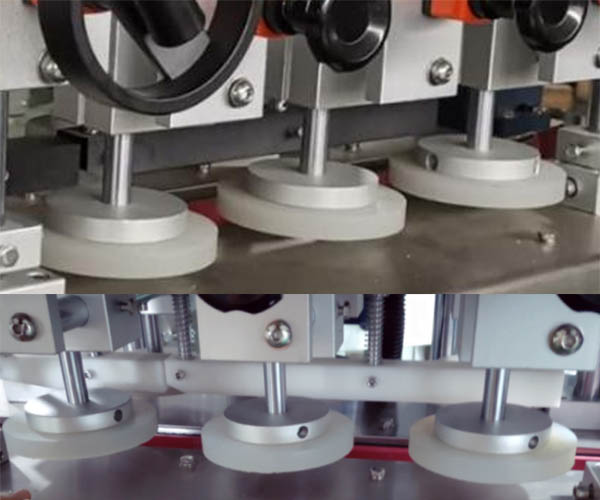
Convenient
Comparing with hand wheel adjustment from other suppliers, one button to raise or lower the whole capping device is much more convenient.
Four switches from left to right are used to adjust speed of bottle conveyor, bottle clamp, cap climbing and bottle separation. The dial can guide the operator to reach suitable speed for each kinds of package easily.
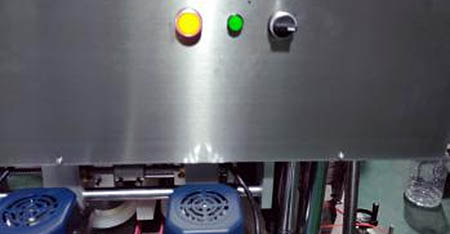
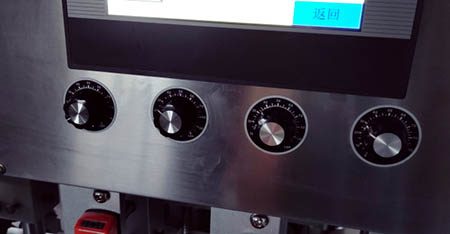
Hand wheels to change distance between two bottle clamp belt easily. There are two wheels at two ends of clamping belt. The dial leads operator to get to the correct position accurately when changing bottle sizes.
Switches to adjust distance between capping wheels and caps. The closer of distance, the tighter the cap will be. Dial helps operator to find a most suitable distance convenient.
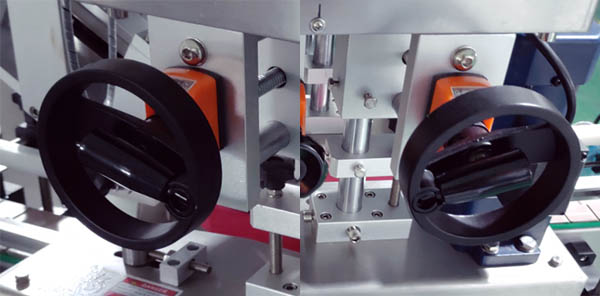
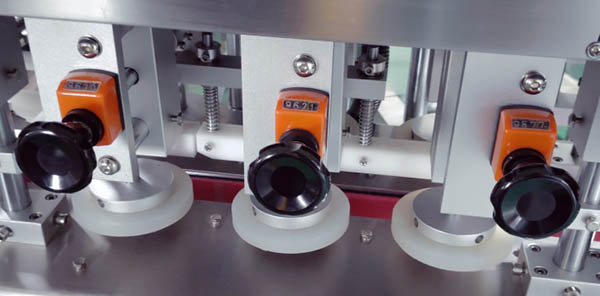
Easy operate
PLC&touch screen control with simple operation program, makes the work easier and more efficient.
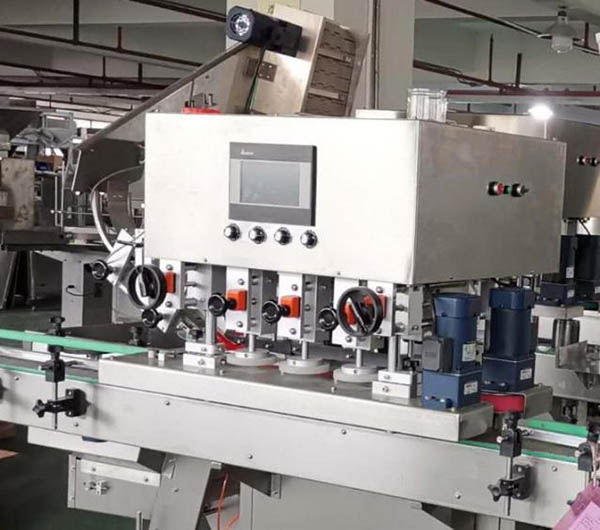
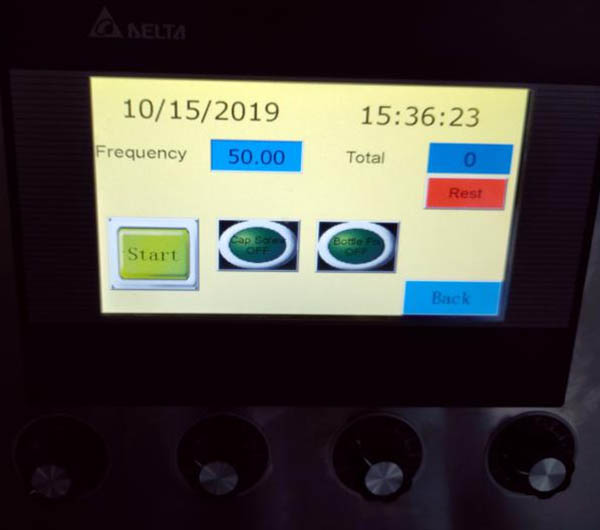
Emergency button to stop the machine at once at urgent moment, which keeps operator staying safe.
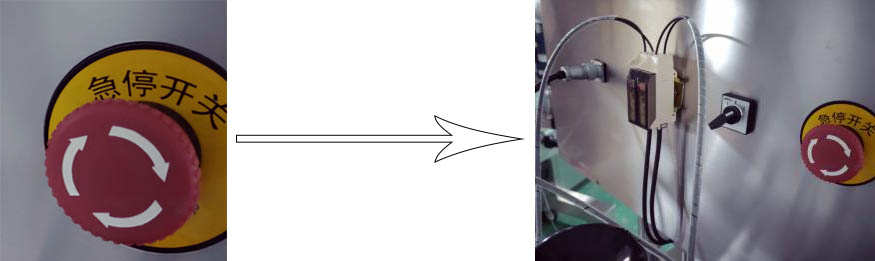
TP-TGXG-200 Bottle Capping Machine |
|||
Capacity |
50-120 bottles/min |
Dimension |
2100*900*1800mm |
Bottles diameter |
Φ22-120mm (customized according to requirement) |
Bottles height |
60-280mm (customized according to requirement ) |
Lid size |
Φ15-120mm |
Net Weight |
350kg |
Qualified rate |
≥99% |
Power |
1300W |
Matrial |
Stainless steel 304 |
Voltage |
220V/50-60Hz(or customized) |
No. |
Name |
Origin |
Brand |
1 |
Invertor |
Taiwan |
Delta |
2 |
Touch Screen |
China |
TouchWin |
3 |
Optronic Sensor |
Korea |
Autonics |
4 |
CPU |
US |
ATMEL |
5 |
Interface Chip |
US |
MEX |
6 |
Pressing Belt |
Shanghai |
|
7 |
Series Motor |
Taiwan |
TALIKE/GPG |
8 |
SS 304 Frame |
Shanghai |
BaoSteel |
The automatic capping machine can work with filling machine and labeling machine to form a packing line.
A. Bottle unscrambler+auger filler+automatic capping machine+foil sealing machine.
B. Bottle unscrambler+auger filler+automatic capping machine+foil sealing machine+labeling machine
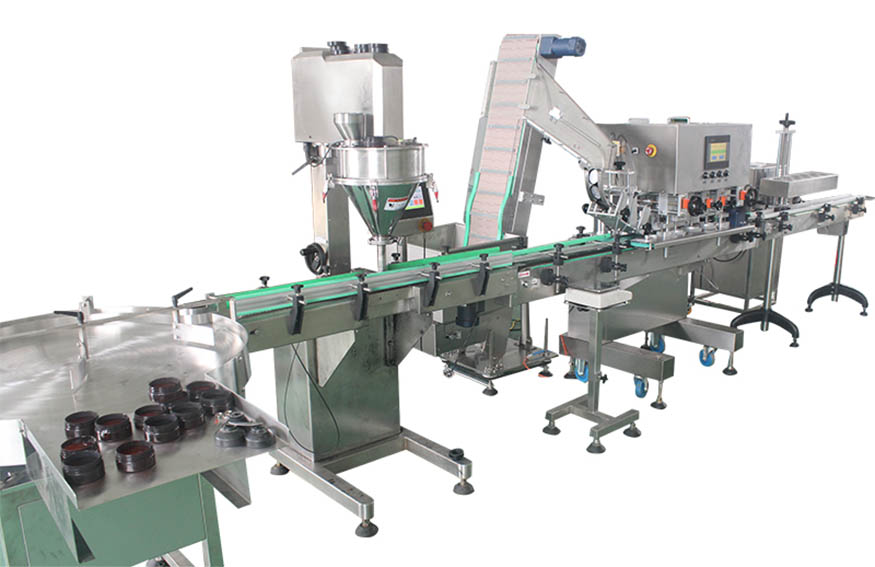
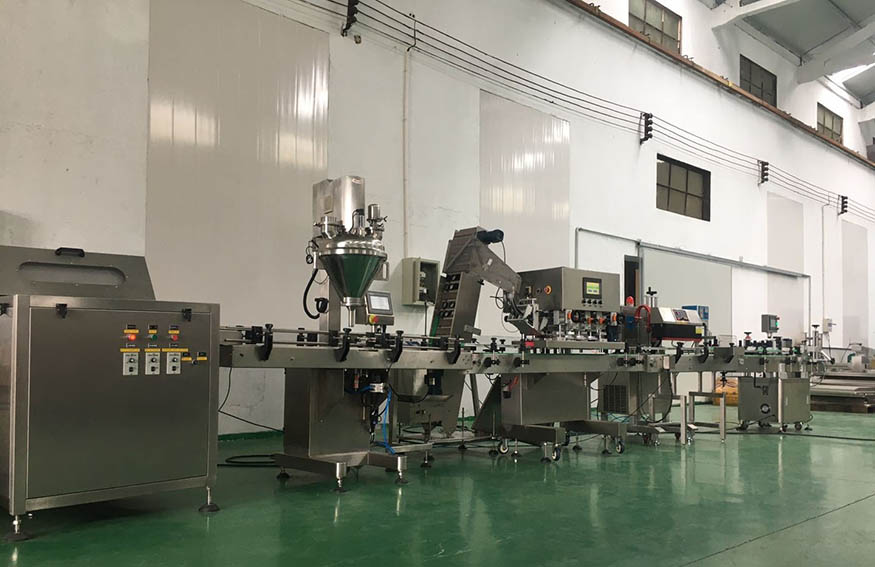
ACCESSORIES in Box
■ Instruction manual
■ Electrical diagram and connecting diagram
■ Safety operation guide
■ A set of wearing parts
■ Maintenance tools
■ Configuration list (origin, model, specs, price)
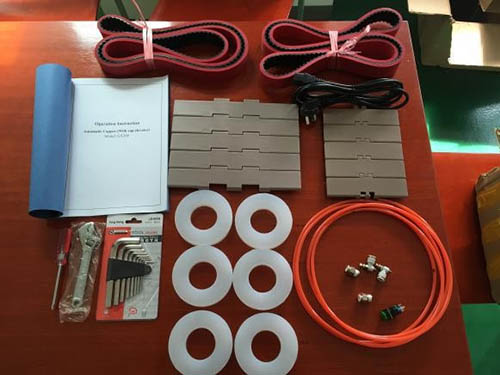
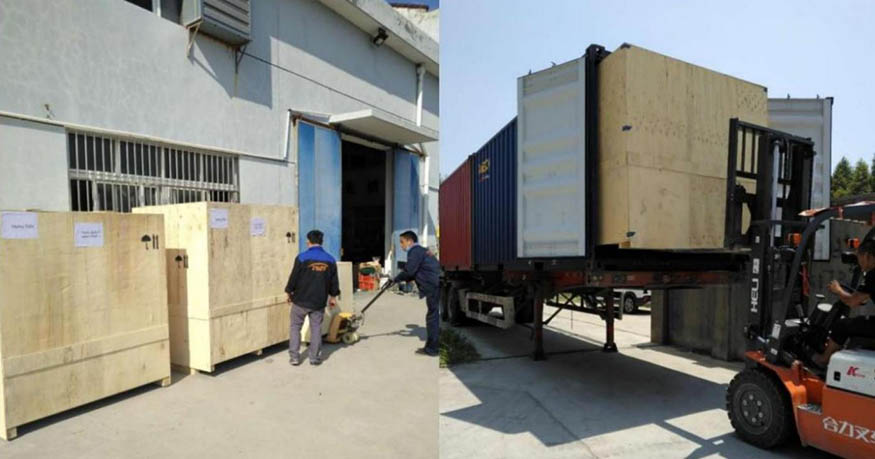
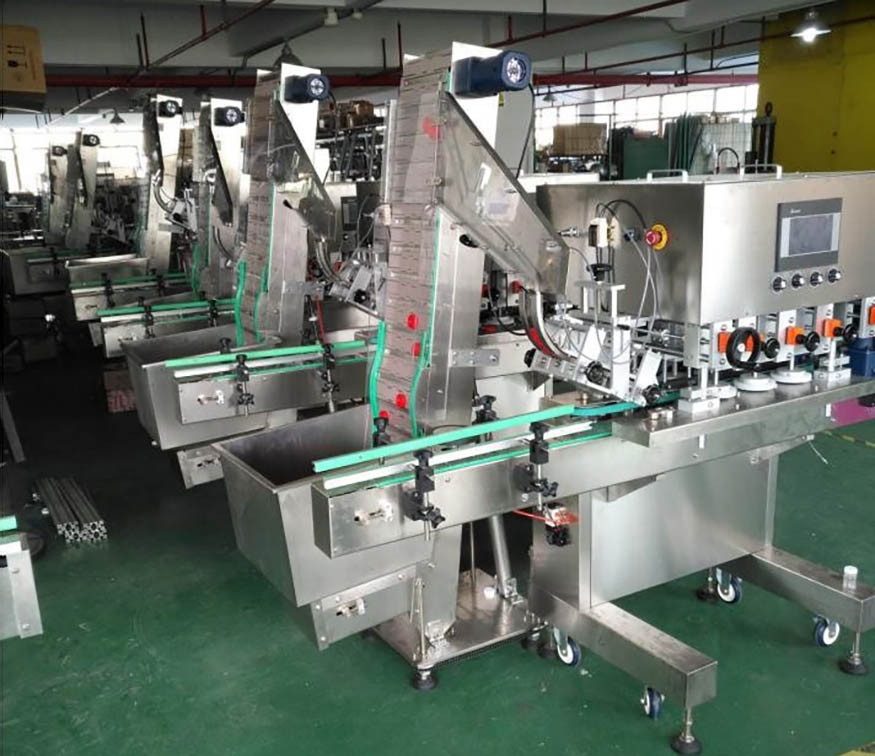
1. Installation of cap Elevator and cap placing system.
(1)Installation of cap arranging and detection sensor.
The cap elevator and placing system is separated before shipping, please install the cap arranging and placing system on capping machine before running the machine. Please connect the system as shown in following pictures:
Lack cap inspection sensor (machine stop)
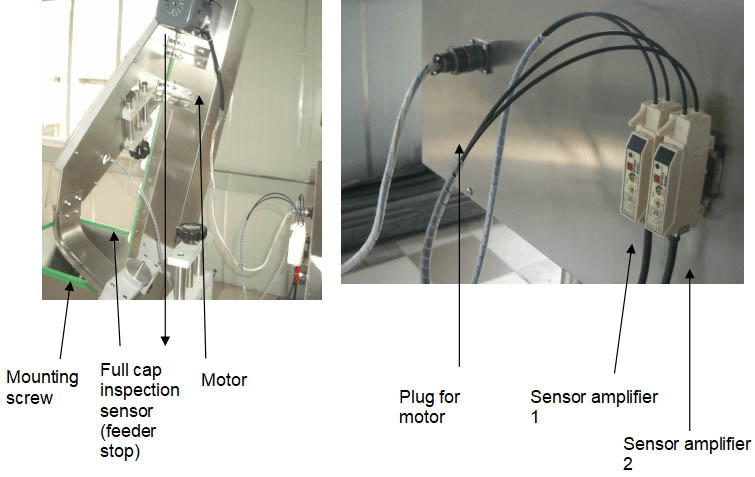
a. Connect the cap placing track and ramp with mounting screw.
b. Connect the motor wire with plug at the right side on control panel.
c. Connect the full cap inspection sensor with the sensor amplifier 1.
d. Connect the lack cap inspection sensor with the sensor amplifier 2.
Adjust the angle of cap climbing chain: The angle of the cap climbing chain has been adjusted according to the sample cap provided by you before shipment. If it is necessary to change the specifications of cap (just change the size, unchanged the type of cap), please adjust the angle of cap climbing chain by angle adjusting screw till the chain can only convey up caps which lean on chain with top side. Indication as following:
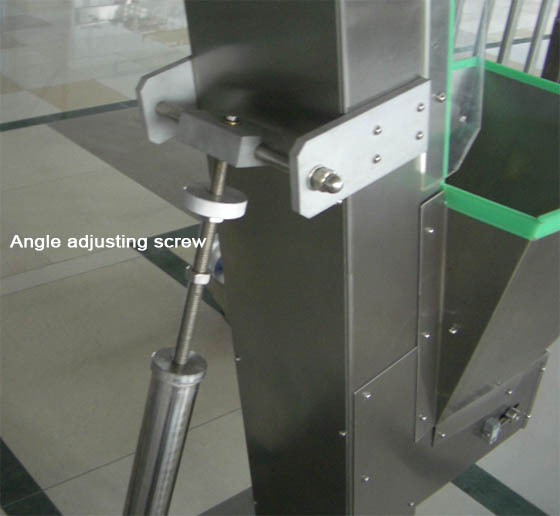
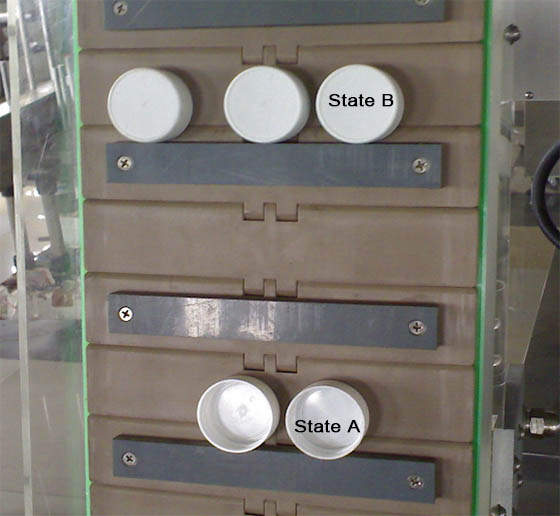
The cap in state A is correct direction when the cap climbing chain bringing caps up.
The cap in state B will drop into tank automatically if the chain is in a proper angle.
(2)Adjust the cap dropping system (chute)
The angle of dropping chute and space has been set already according to sample provided. Normally if there's no other new specification of bottle or cap, the setting needs not to be adjusted. And if there are more specifications than 1 specification of bottle or cap, client need to list the item on contract or its attachment to ensure manufactory leave enough space for further modifications. The method of adjustment is as following:
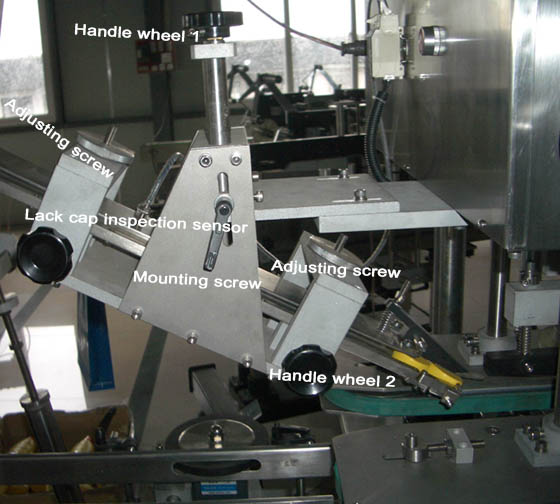
Adjust the height of cap dropping system: Please loose the mounting screw before turn the handle wheel 1.
The adjusting screw can adjust the height of space of chute.
The handle wheel 2 (on two sides) can adjust the width of space of chute.
(3) Adjusting the cap pressing part
The cap will cover the bottle mouth from the chute automatically when the bottle is feeding into the area of cap pressing part. The cap pressing part can also be adjusted due to the height of bottles and caps. It will affect the capping performance if the pressure on the cap is not suitable. If the position of cap press part is too high, the pressing performance will be influenced. And if the position is too low, the cap or bottle will be damaged. Normally the height of cap pressing part has been adjusted before shipment. If user need adjust the height, the method of adjustment is as following:
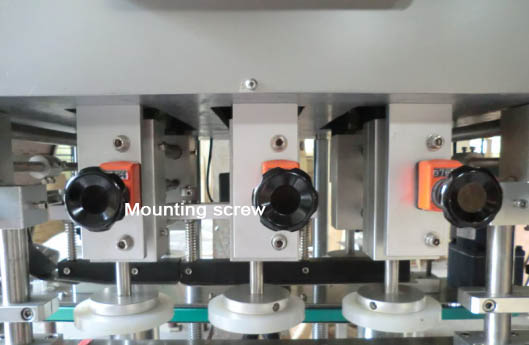
Please loose the mounting screw before adjust the height of cap pressing part.
There is another cap pressing part with the machine to fit the smallest bottle ,the way of change it is shown in the video.
(4). Adjusting the air pressure to blow the cap into the chute.
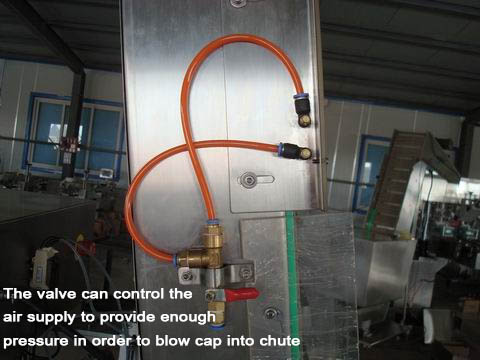
2. Adjusting the height of main parts as a whole.
The height of main parts such as bottle fix structure, gum-elastic spin wheel, cap pressing part can be adjusted as a whole by machine elevator. The control button of machine elevator is on the right side of control panel. User should loose the mounting screw on the two support pillar before start the machine elevator.
ø means down and ø means up. To make sure the position of spin wheels is match with caps. Please shut off the elevator power and fasten the mounting screw after adjustment.
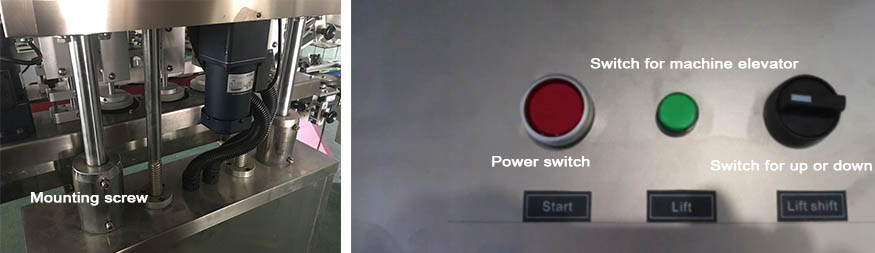
Remark: Please press the lift switch (green) all the time until getting the right position. The speed of elevator is very slowly, please be waiting for patiently.
3. Adjust the gum-elastic spin wheel (three pairs of spin wheel)
The height of spin wheel is adjusted by the machine elevator.
The width of pair of spin wheel is adjusted according the diameter of cap.
Normally the distance between a pair of wheel is 2-3mm less than the diameter of cap. Operator can adjust the width of spin wheel by handle wheel B. (each handle wheel can adjust relative spin wheel).
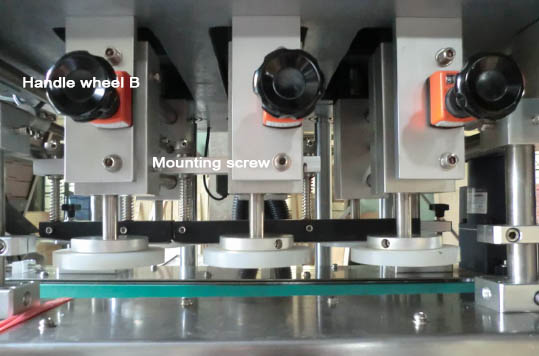
Please loose the mounting screw before adjustment the handle wheel B.
4. Adjusting the bottle fix structure.
The fix position of the bottle can be adjusted by adjusting the position of fix structure and link axis. If the fix position is too low on the bottle, the bottle easy to lay down during feeding or capping. On the contrary if the fix position is too high on the bottle, it will disturb the proper working of spin wheels. Be sure that the centerline of conveyor and bottle fix structures are on the same line after adjustment.
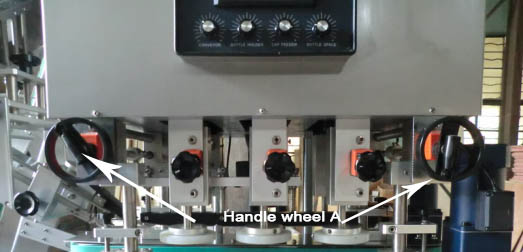
Turning handle wheel A (to turn the handle by 2 hands together) to adjust the distance between bottle fix belt. So the structure could fix the bottle well during pressing process.
The height of bottle fix belt is usually adjusted by the machine elevator.
(Caution: Operator can adjust the height of bottle fix belt in a micro-scope after loose the mounting screw on 4 link shaft.)
If operator need move fix belt in a big range, please adjust the position of belt after loosen screw 1 and screw 2 together, and if operator need adjust height of belt in a small range, please loose screw 1 only, and turn the adjustment knob.
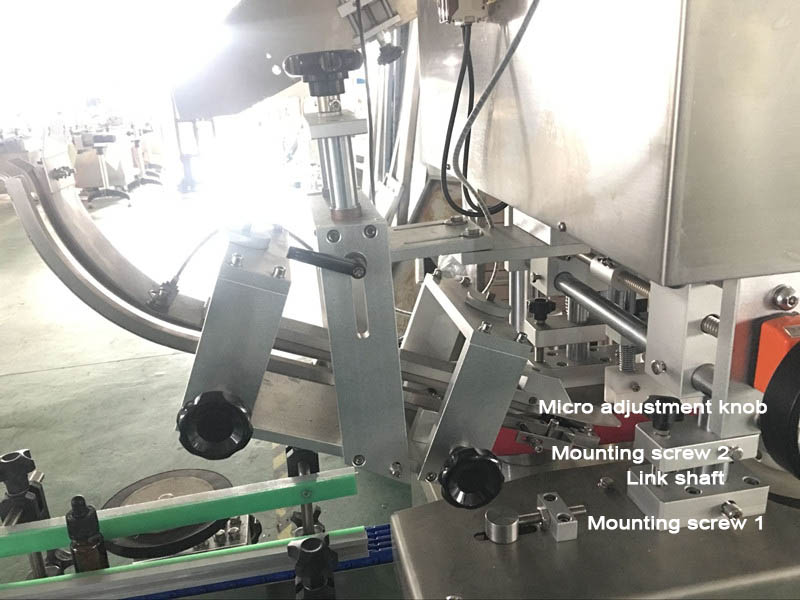
5. Adjusting the bottle space adjusting wheel and railing.
Operator should change the position of bottle space adjusting wheel and railing when replacing the specification of bottle. The space between the space adjusting wheel and railing should 2-3mm less then the diameter of bottle. Please be sure that the centerline of conveyor and bottle fix structures are on the same line after adjustment.
Loosen adjusting screw can adjust the position of bottle space adjusting wheel.
Loose adjusting handle can adjust the width of railing on the both sides of conveyor.
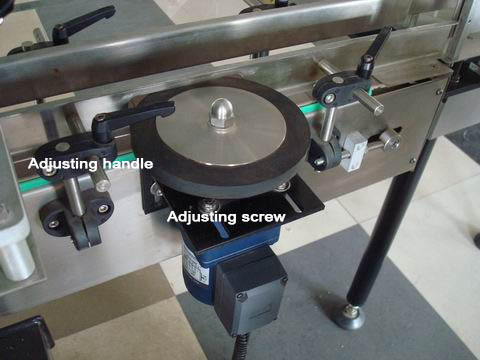