With a horizontal U-shaped design, the ribbon mixing machine can effectively combine even the tiniest amount of material into massive batches. It is particularly useful for mixing powders, powder with liquid, and powder with granules. It can also be used in construction, agriculture, food, plastics, pharmaceuticals, etc. For an effective procedure and result, ribbon mixing machine provides versatile and highly scalable mixing.
Here are the main features:
- All connected parts are well-welded.
- The tank's interior is a full mirror polished with ribbon and shaft.
-Stainless steel 304 is used in all parts.
- When mixing, there are no dead angles.
- The shape is round with a silicone ring lid feature.
- It has a safe interlock, a grid, and wheels.
The ribbon mixing machine's structural components are as follows:
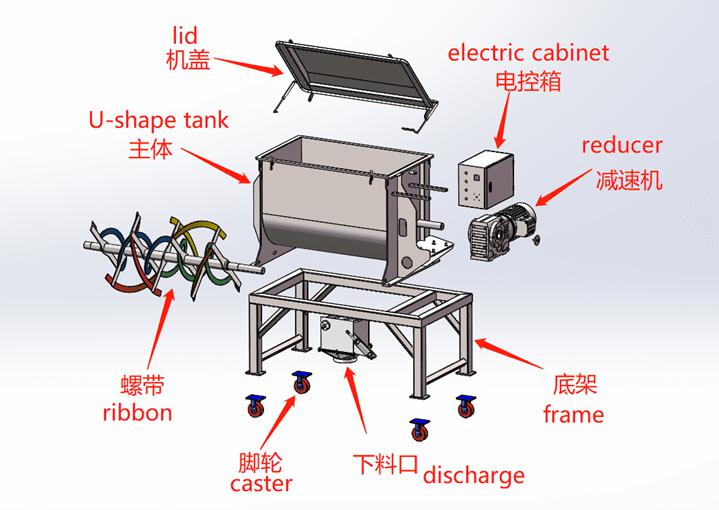
Note:
Lid/Cover - A lid, usually known as a cover, is a portion of a container which provides as the machine closure or seal.
U Shape Tank- A horizontal U-shaped tank that serves as the body of the machine and where the mixing happens.
Ribbon- Ribbon mixing machine has ribbon agitator. The ribbon agitator is made up of inner and outer helical agitator that is effective for mixing materials.
Electric Cabinet- It is where the switching on and off power, discharge switch, emergency switch, and mixing timer are placed.
Reducer- The reducer box drives the shaft of this ribbon mixer, and the ribbons of the shaft move the materials up and down.
Caster- An undriven wheel is installed at the bottom of the machine to facilitate movement of the ribbon mixing machine.
Discharge- When the materials are mixed, discharge valves are used to quickly release materials, leaving no residues.
Frame- The tank of the ribbon mixing machine is supported by a frame that keeps it in place.
Here's how a ribbon mixing machine works effectively and efficiently:
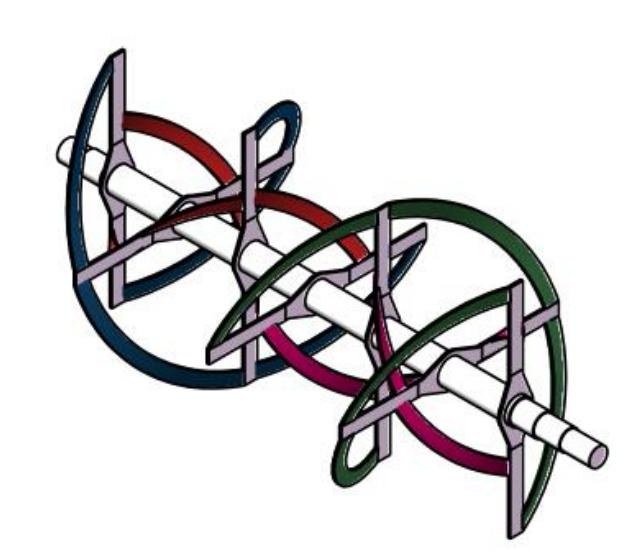
For highly balanced mixing of materials, the ribbon mixing machine has a ribbon agitator and a U-shaped chamber.
The ribbon agitator is made up of inner and outer helical agitators. When moving materials, the inner ribbon moves the material from the center to the outside, while the outside ribbon moves the material from two sides to the center, and it is combined with rotating direction.
It provides a faster mixing time while also producing a better mixing effect.
Discharge Types of Valves
-The ribbon mixing machine has optional valves such as flap valves, butterfly valves, etc.
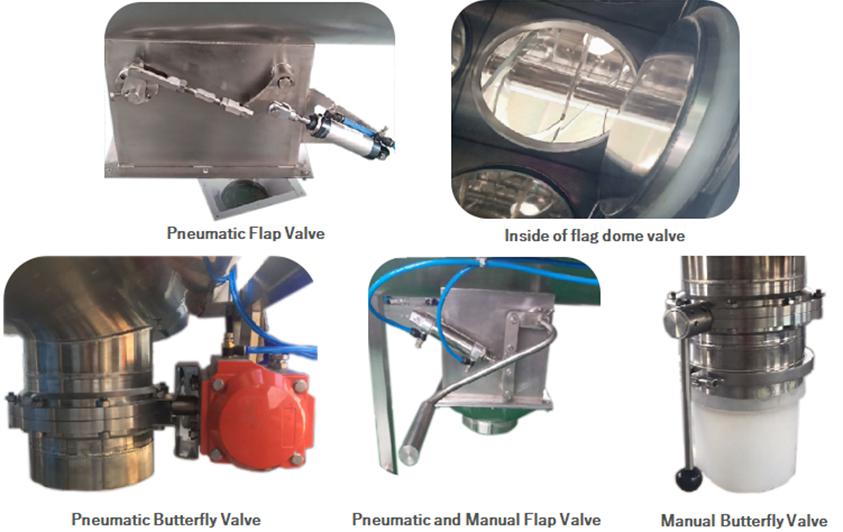
When it comes to customizing your ribbon mixing machine, how your materials discharge from the mixer is important. Here's the application of discharge type:
The ribbon mixing machine discharge valve can be driven manually or pneumatically.
Pneumatic: a type of function that allows for accurate output adjustment. Pneumatic operation for releasing material includes quick release and no leftovers.
Manual: Controlling the discharge amount is easier with a manual valve. It's also suitable for materials with bag flowing.
Flap valve: Flap valves are the ideal choice for discharge since it minimize residue and limit the amount that wasted.
Butterfly valve: are commonly used for semi-liquid materials. It provides the best tight seal, and there’s no leakage.
Material and application that is widely used in the industry:
For dry solid blending and liquid materials, it is commonly used in the following industries:
Pharmaceutical industry: mixing prior to powders and granules.
Chemical industry: metallic powder mixtures, pesticides, herbicides, and many more.
The food processing industry: cereals, coffee mixes, dairy powders, milk powder, and many more.
Construction industry: steel preblends, etc.
Plastics industry: mixing of masterbatches, mixing of pellets, plastic powders, and many more.
Polymers and other industries.
Ribbon mixing machines are currently common in many industries.
I hope this blog will provide you with some ideas and help you with your ribbon mixing machine application.
Post time: Jan-26-2022