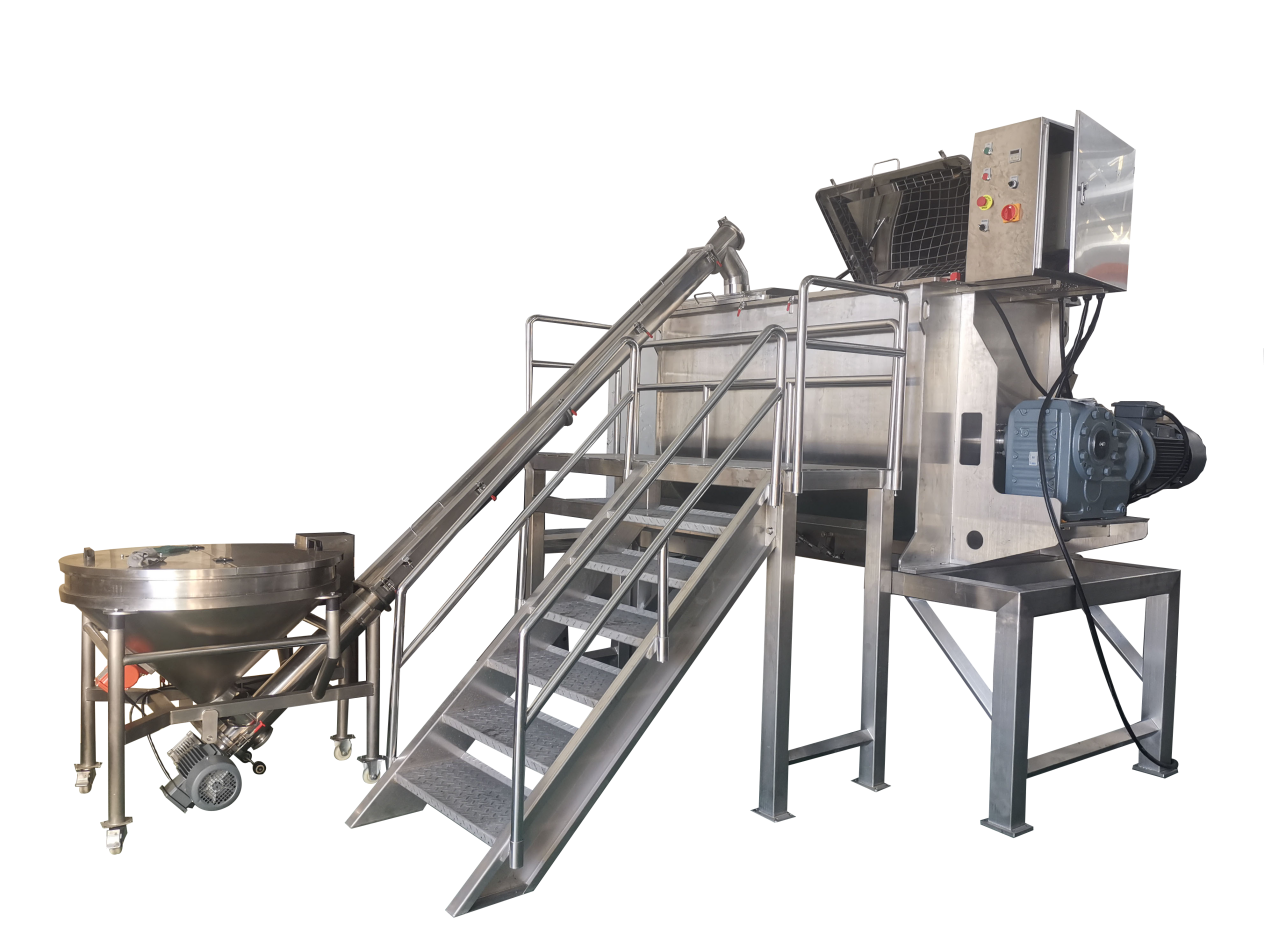
A ribbon blender is an efficient mixing machine widely used in industries like chemicals, pharmaceuticals, and food processing. It is designed for mixing both solid-solid (powdered materials, granular materials) and solid-liquid (powder and flowable materials) combinations.
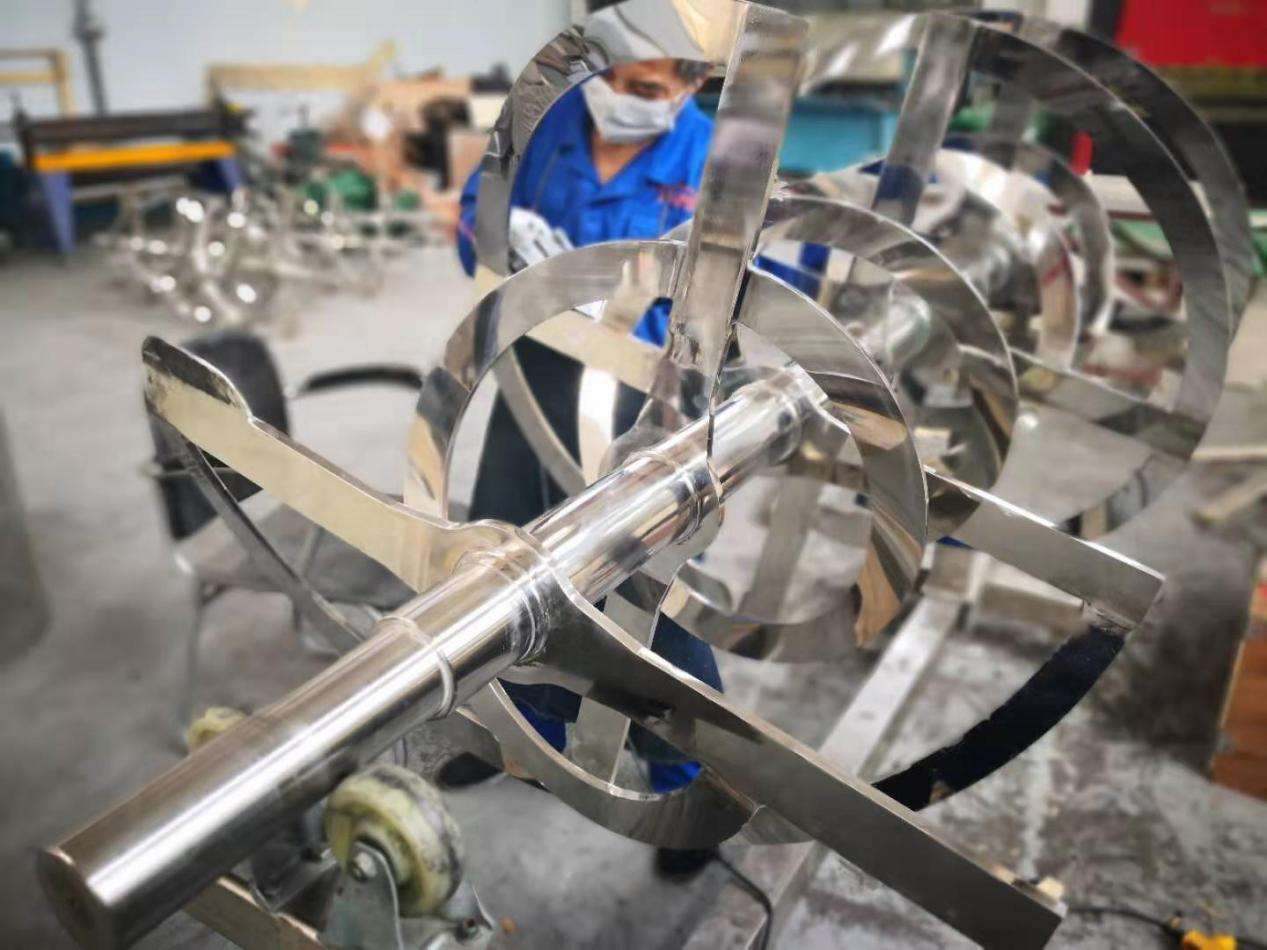
Consisting of a mixing container, spiral ribbons, and a drive system, it revolutionizes traditional mixing processes, making them faster, more efficient, and easier to clean. Named after its ribbon-shaped blades, the blender moves materials through a U-shaped trough to ensure thorough mixing. It is versatile enough for both dry and wet mixing, making it a key tool in industries like food processing, pharmaceuticals, chemicals, and construction.
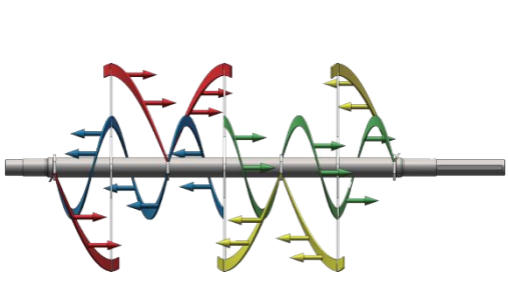
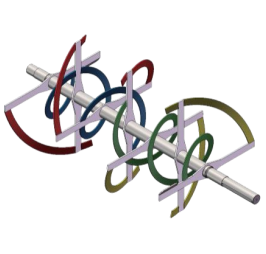
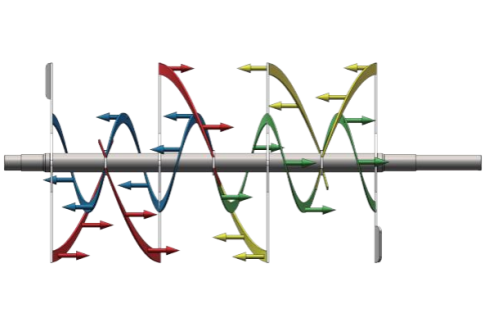
A ribbon blender works on the principle of creating a consistent mixing action through two interlocking helical ribbons that rotate in opposite directions. The outer ribbon moves material toward the center, while the inner ribbon moves it outward. This dual action creates a gentle yet effective blending process, allowing for a uniform distribution of ingredients, even when they have varying densities or particle sizes. The shape and movement of the ribbons ensure both horizontal and vertical mixing, making it ideal for dry powders, granular materials, and some wet blends. Following link to help you better understand the ribbon blender principle.
What is the principal of ribbon blender?
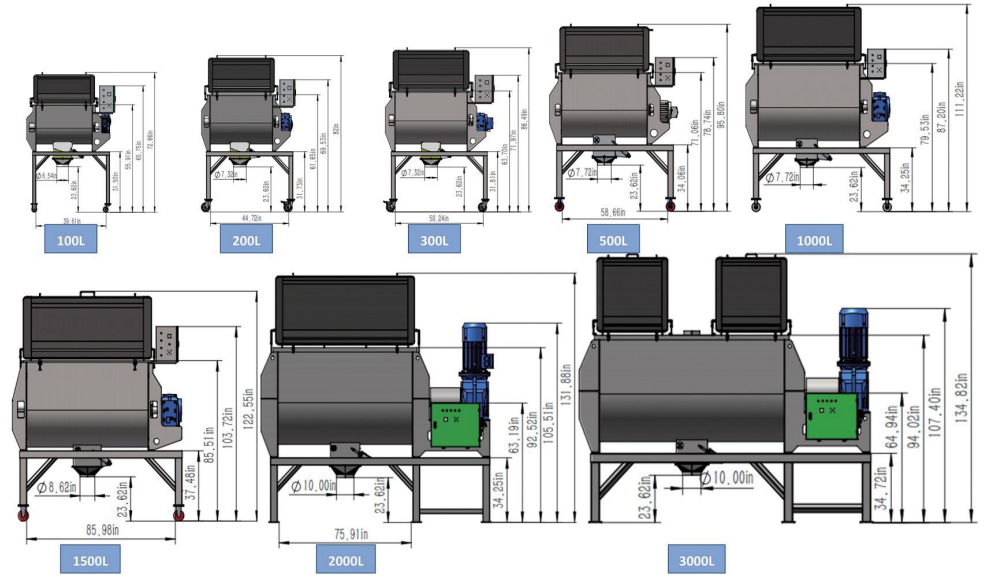
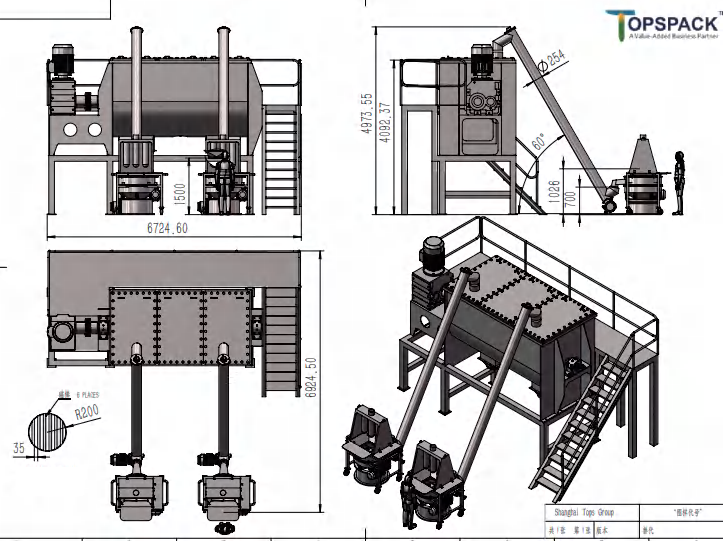
Ribbon blenders typically range in mixing volume from 40L to 14,000L. Models under 100L are commonly used for market trials or formula testing, allowing manufacturers to experiment with different blends in smaller quantities. The 300L to 1000L models are the most popular due to their versatility, as they strike a balance between capacity and output, making them ideal for many manufacturing needs.
When selecting a ribbon blender, the key factor is determining how many kilograms of product you need to mix per batch. On average, there are typically two batches per hour. You can refer to the following blogs for a deeper understanding of how to choose the right model based on your production needs.
How full can you fill a ribbon blender?
How do l select a ribbon blender?
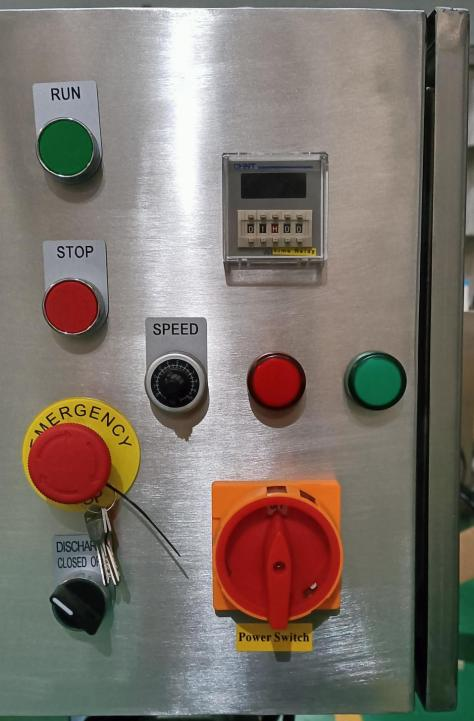
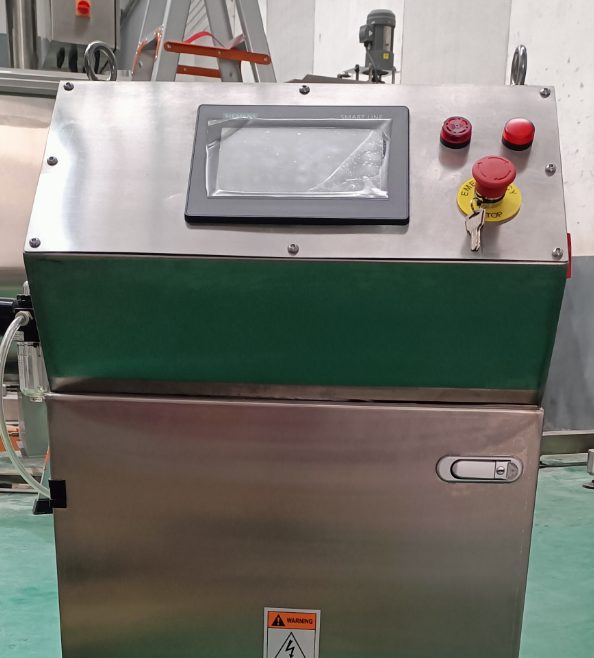
The operation of a ribbon blender is straightforward, with most models featuring just a few essential controls such as power, emergency stop, run, stop, discharge, and time settings. In more customized versions, especially those with additional functions like heating, weighing, or spraying, the blender may be equipped with a PLC (Programmable Logic Controller) and a touchscreen for enhanced control. Even with the touchscreen, the interface is typically user-friendly and easy to navigate.
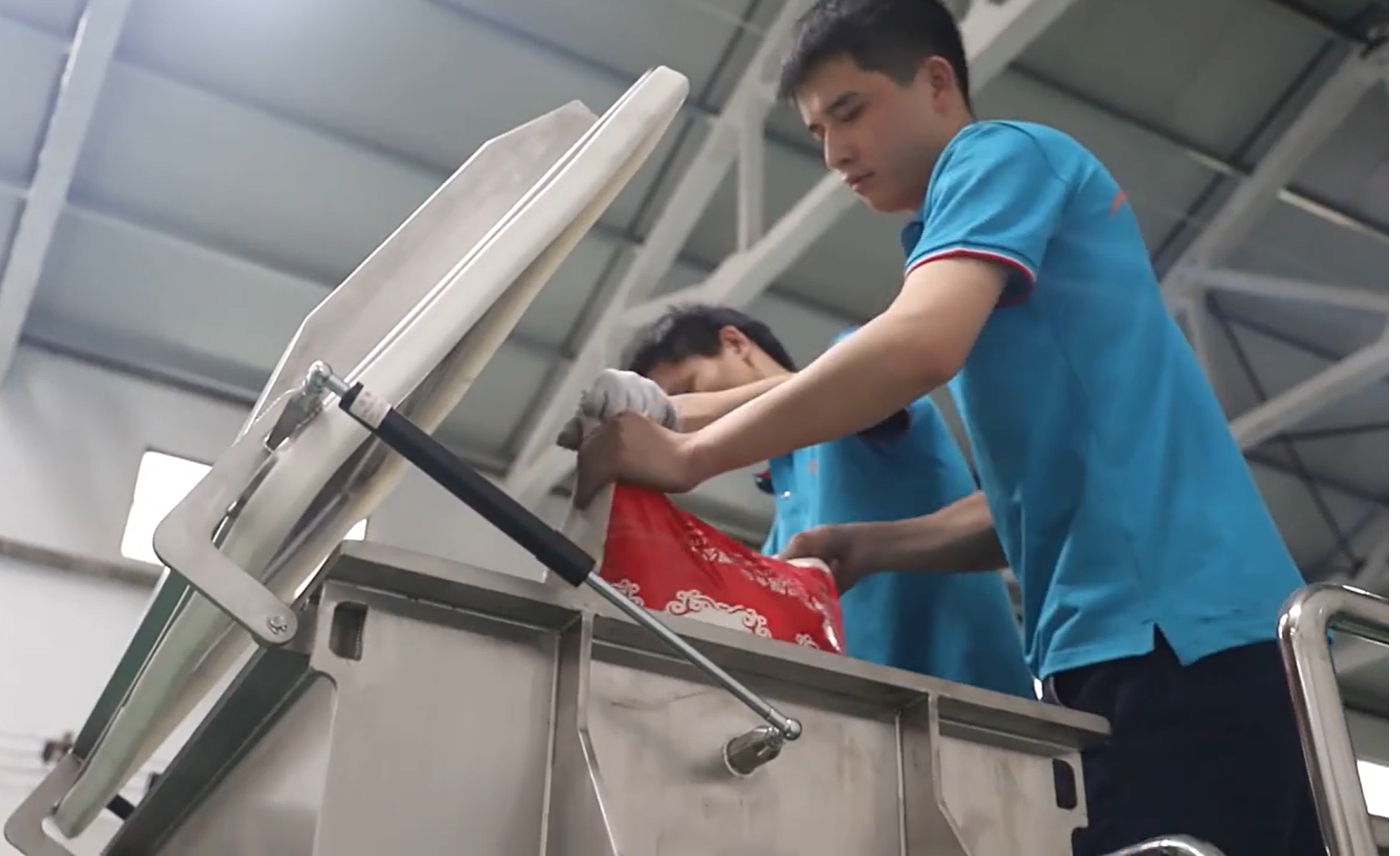
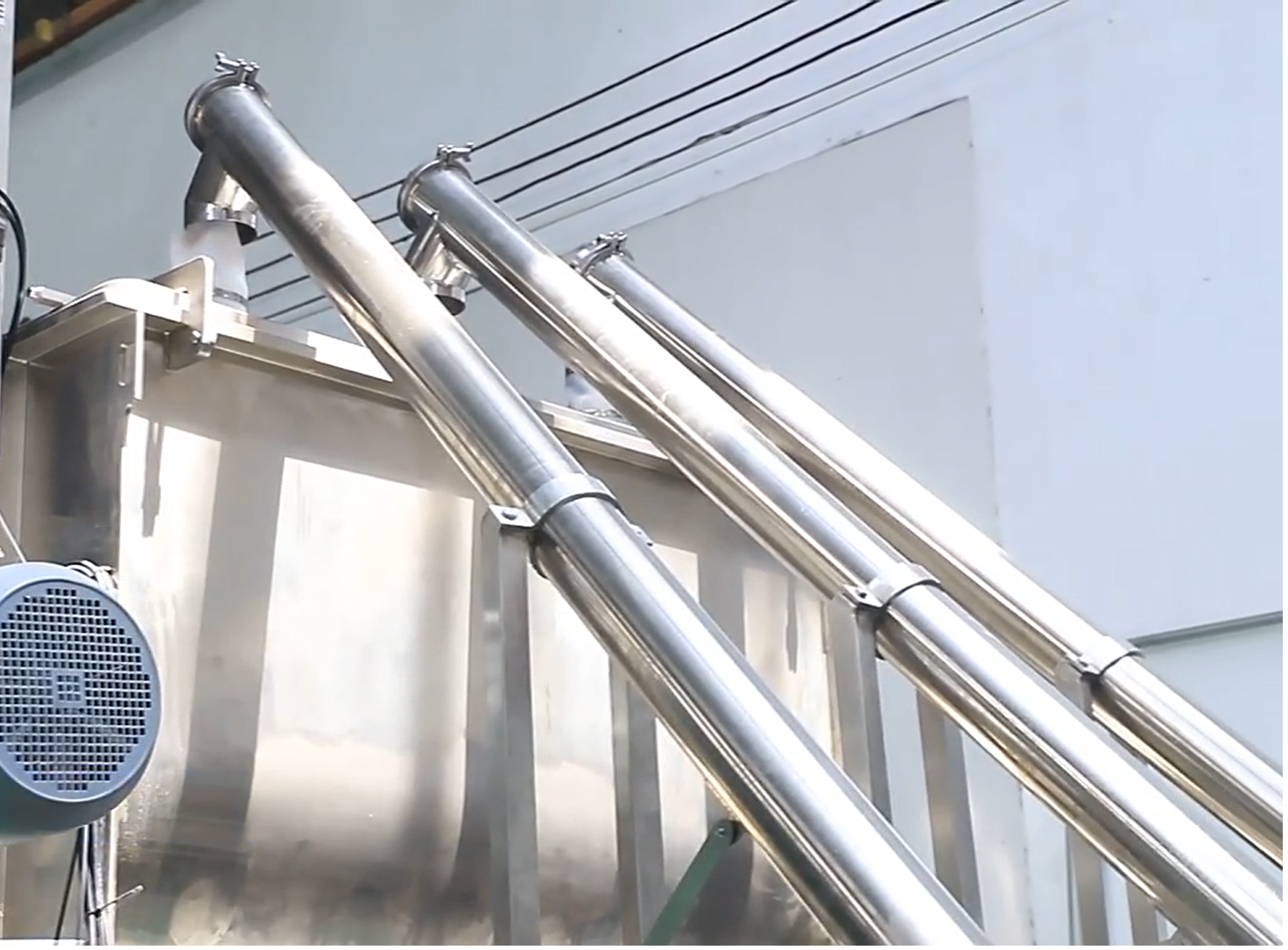
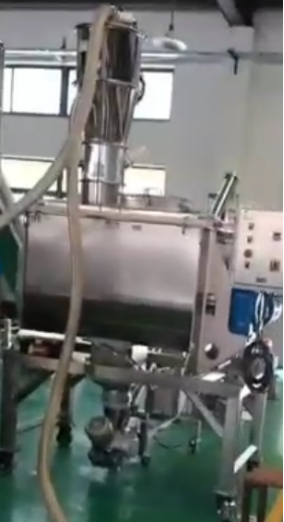
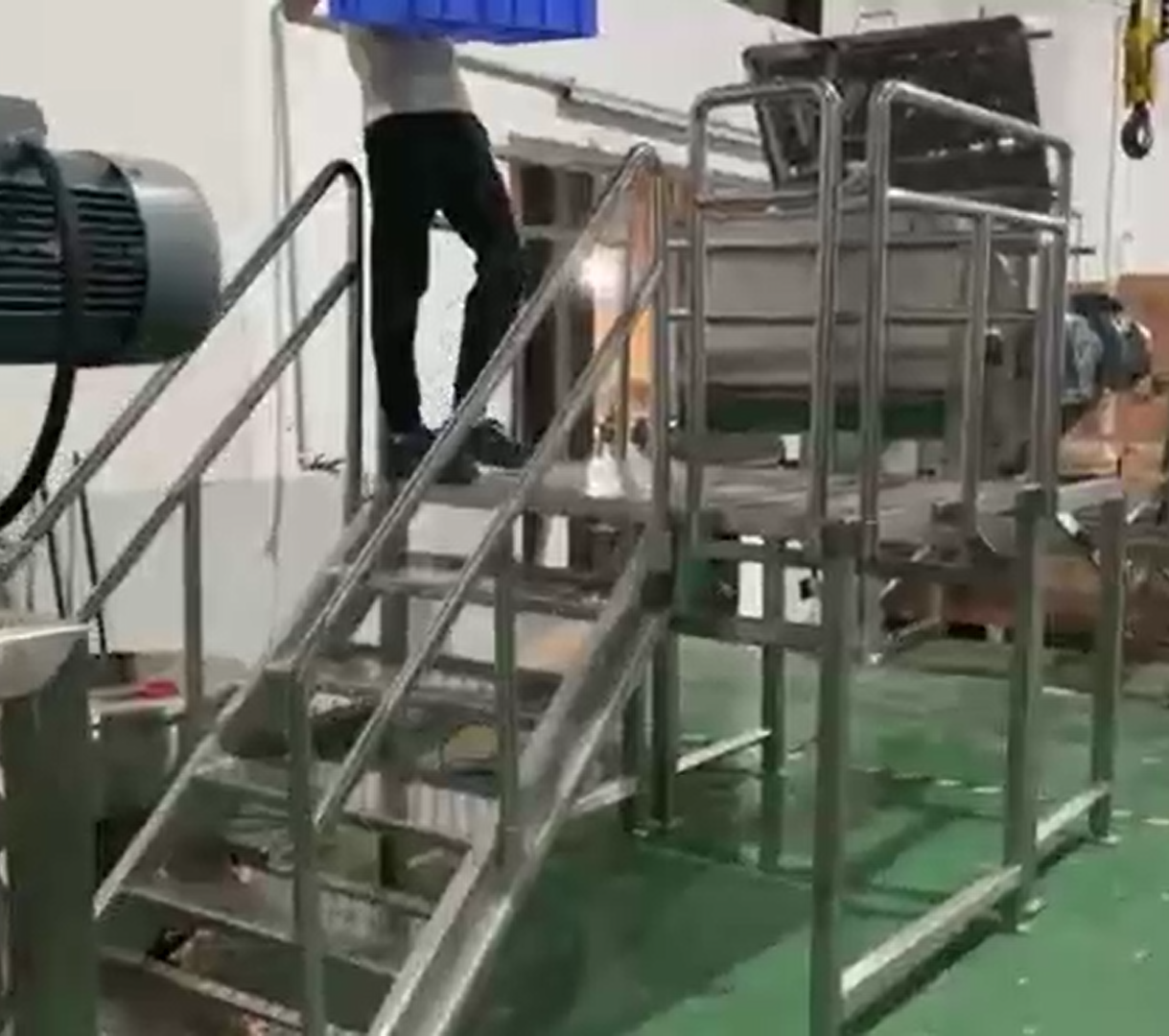
The loading process of a ribbon blender can be either manual or automatic. In manual loading, the operator pours the materials into the blender by hand. In automatic loading, a feeding system or machine automatically delivers the ingredients into the blender, reducing manual labor. For a better understanding of these loading types, you can refer to the following blog links.
Moreover, the ladder and platform is necessary for ribbon blender cleaning and maintain.
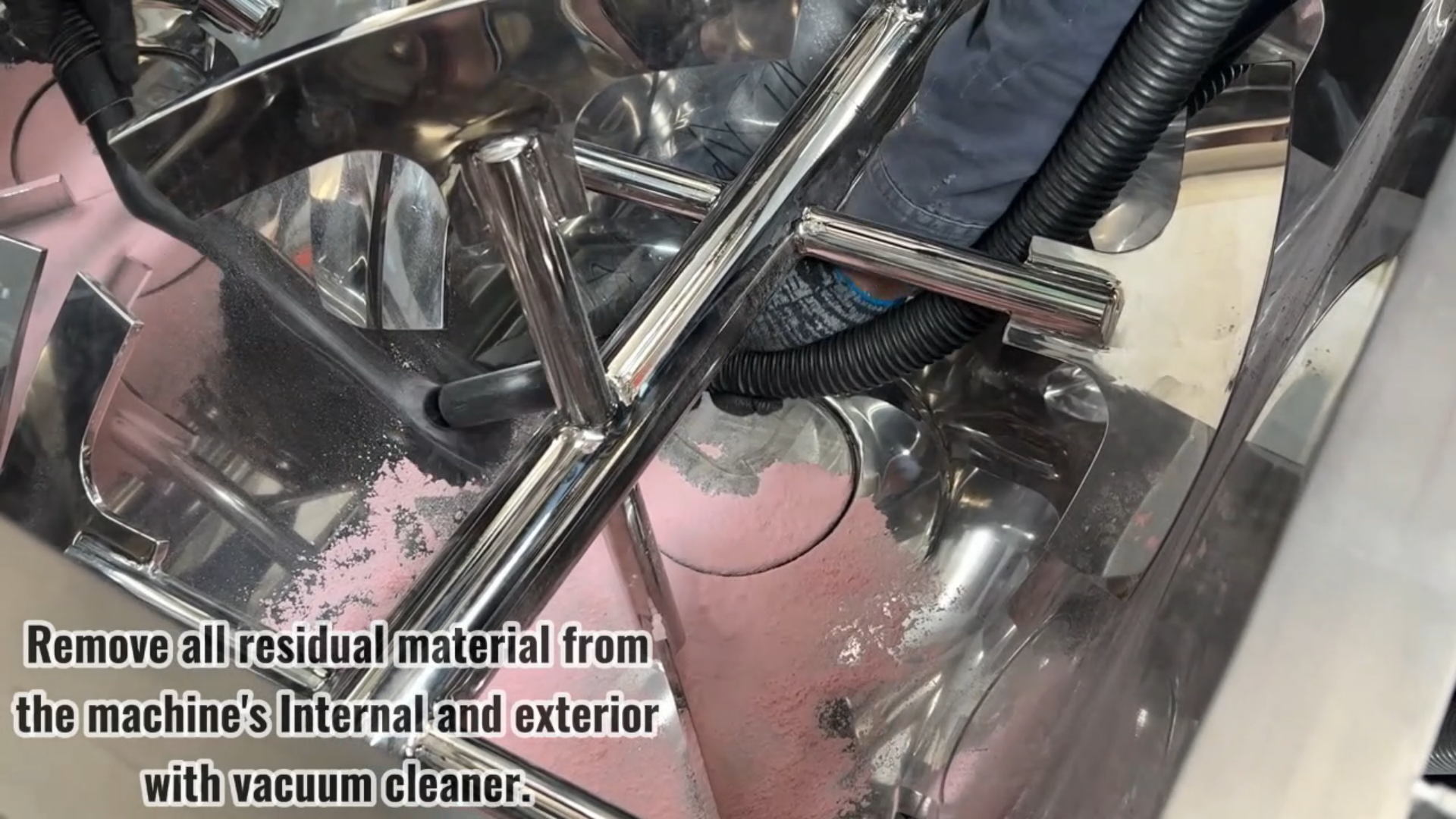
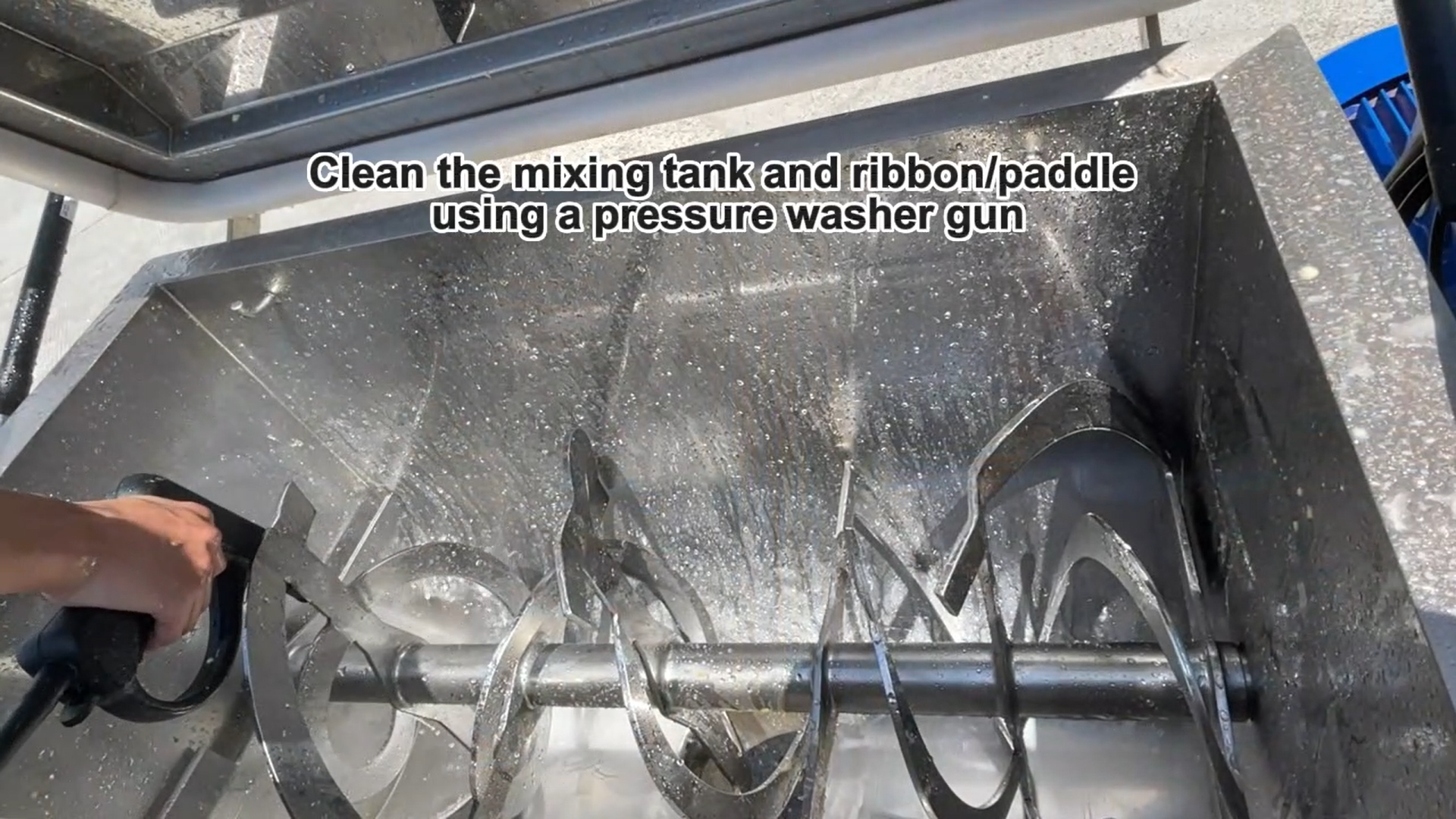
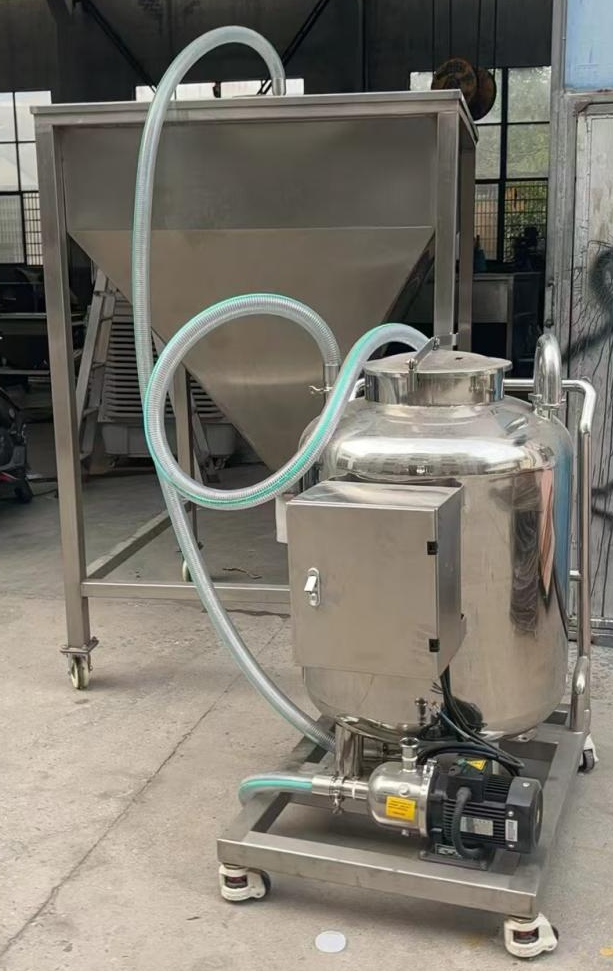
Cleaning and maintenance of a ribbon blender are relatively simple. For a quick clean, an air gun can effectively remove loose material. For a more thorough cleaning, a water gun is typically used. To save time and energy, a CIP (Clean-in-Place) system can be highly effective, as it automates much of the cleaning process.
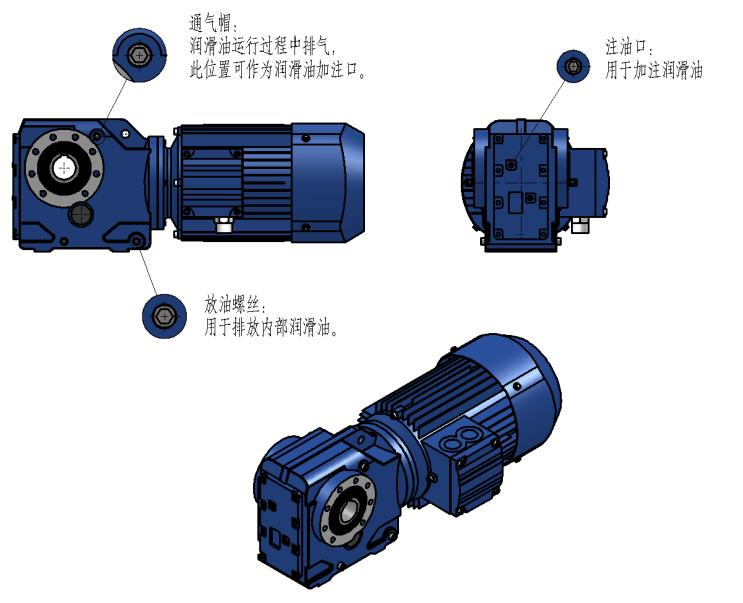
Maintenance mainly involves adding or changing the lubricating oil, replacing silicone seals, and ensuring proper shaft sealing. These tasks are straightforward but essential for keeping the blender running smoothly.
For more details or any questions, feel free to reach out to us. We are committed to answering your inquiries within 24 hours.
Post time: Feb-27-2025