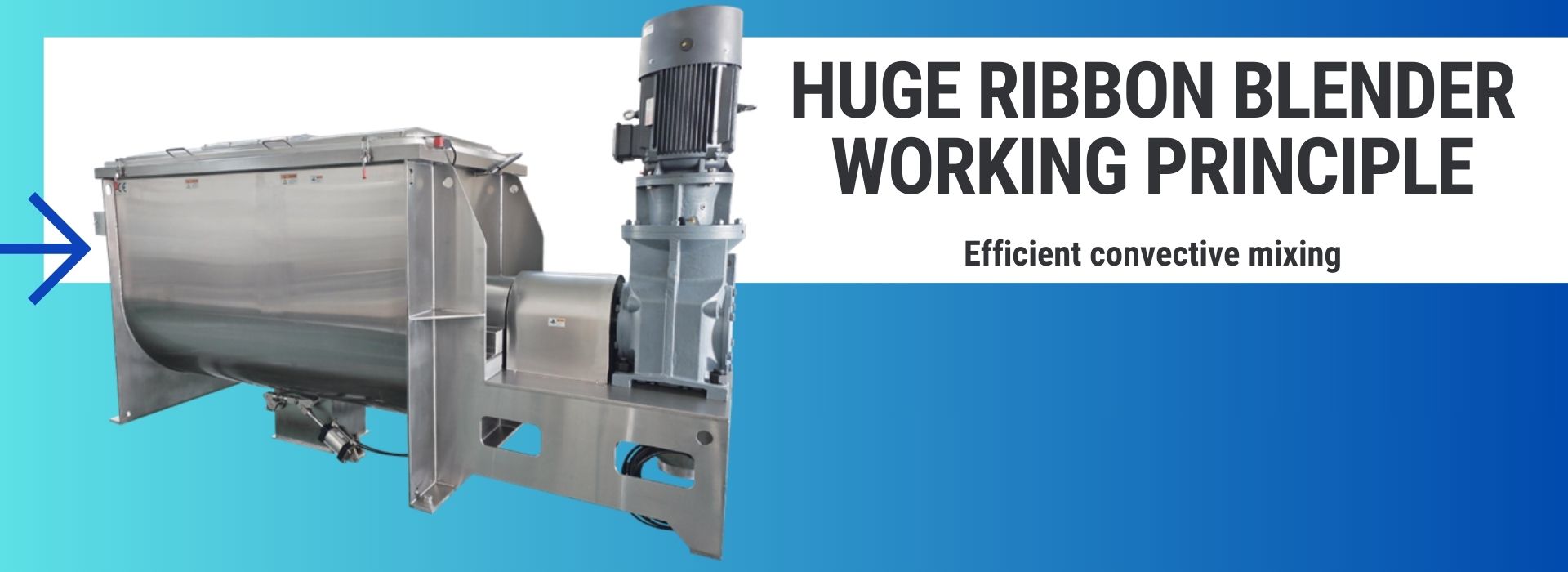
What is the huge Industrial Size Blender?
The industrial size blender finds widespread use across multiple industries, including construction, food processing, chemicals, and pharmaceuticals. It is used to blend powder with liquid, powder with granules, and powder with other powder. The twin ribbon agitator, which is powered by a motor, speeds up the convective mixing of ingredients.
This is a brief description of industrial size blender working principle:
The mixer's design:
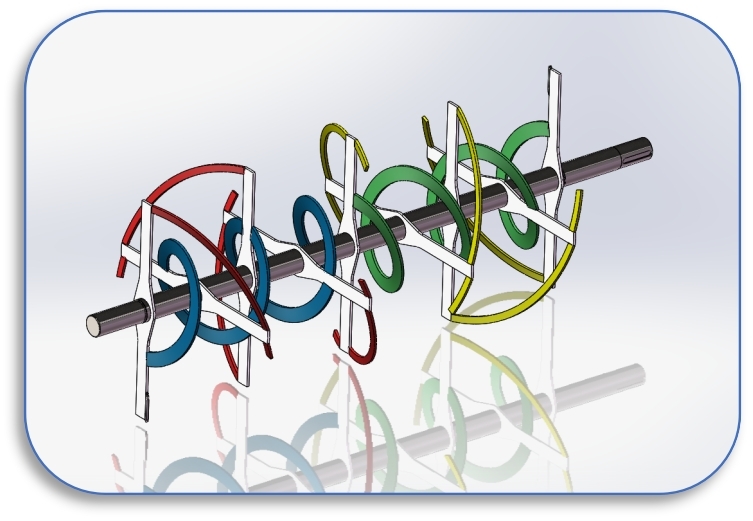
A U-shaped chamber with a ribbon agitator allows for extremely balanced material mixing in a ribbon blender. The inner and outer helical agitators comprise the ribbon agitator.
Compiling Components:
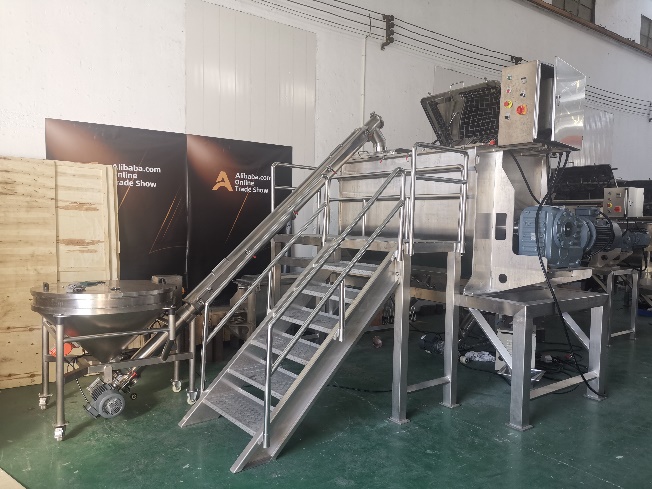
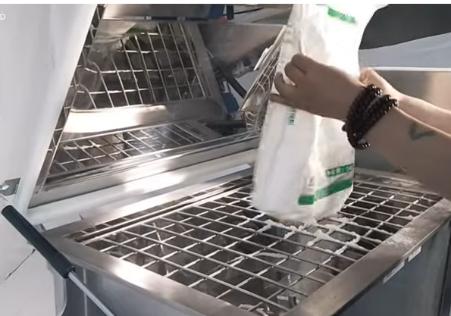
Industrial size blender comes with either a non-automated loading system that involves manually pouring the components into the top aperture or an automated loading system that links the screw feeding.
Procedure for Mixing:
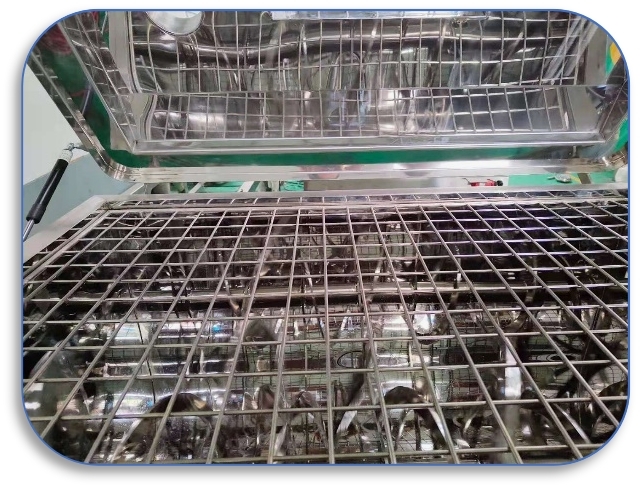
The mixing is started after the ingredients are loaded. When moving materials, the inner ribbon carries them from the center to the outside, and the outside ribbon transports them from one side to the center while also spinning in the opposite direction. A ribbon blender produces superior mixing results in a shorter amount of time.
Continuity:
One U-shaped horizontal mixing tank and two sets of mixing ribbons make up the system; the outer ribbon moves the powder from the ends to the center, while the inner ribbon does the opposite. Homogeneous mixing is the outcome of this countercurrent activity.
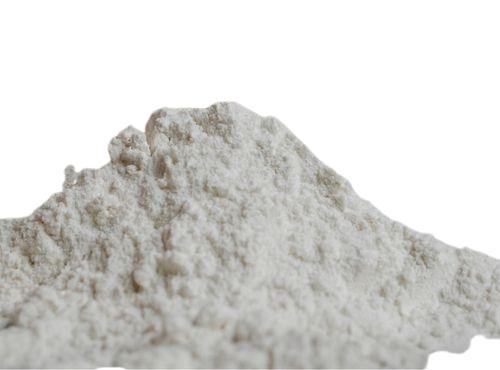
Discharge:
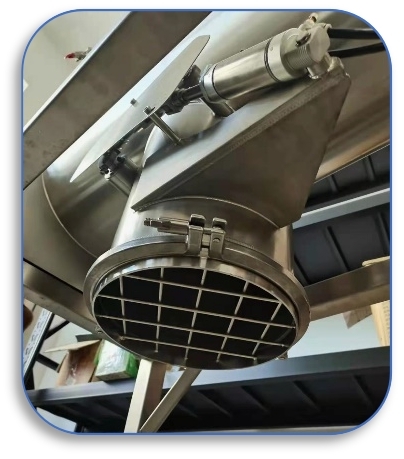
The blended material gets discharged at the tank's bottom when mixing is finished, attributable to a center-mounted flap dome valve that has manual and pneumatic control options. During the mixing process, the valve's arc design guarantees that no material accumulates and removes any potential dead angles. The reliable and steady sealing mechanism stops leaks when the valve is opened and closed often.
Specification:
Model |
TDPM 100 |
TDPM 200 |
TDPM 300 |
TDPM 500 |
TDPM 1000 |
TDPM 1500 |
TDPM 2000 |
TDPM 3000 |
TDPM 5000 |
TDPM 10000 |
Capacity(L) |
100 |
200 |
300 |
500 |
1000 |
1500 |
2000 |
3000 |
5000 |
10000 |
Volume(L) |
140 |
280 |
420 |
710 |
1420 |
1800 |
2600 |
3800 |
7100 |
14000 |
Loading rate |
40%-70% |
|||||||||
Length(mm) |
1050 |
1370 |
1550 |
1773 |
2394 |
2715 |
3080 |
3744 |
4000 |
5515 |
Width(mm) |
700 |
834 |
970 |
1100 |
1320 |
1397 |
1625 |
1330 |
1500 |
1768 |
Height(mm) |
1440 |
1647 |
1655 |
1855 |
2187 |
2313 |
2453 |
2718 |
1750 |
2400 |
Weight(kg) |
180 |
250 |
350 |
500 |
700 |
1000 |
1300 |
1600 |
2100 |
2700 |
Total Power (KW) |
3 |
4 |
5.5 |
7.5 |
11 |
15 |
18.5 |
22 |
45 |
75 |
Choices for Extra Features:
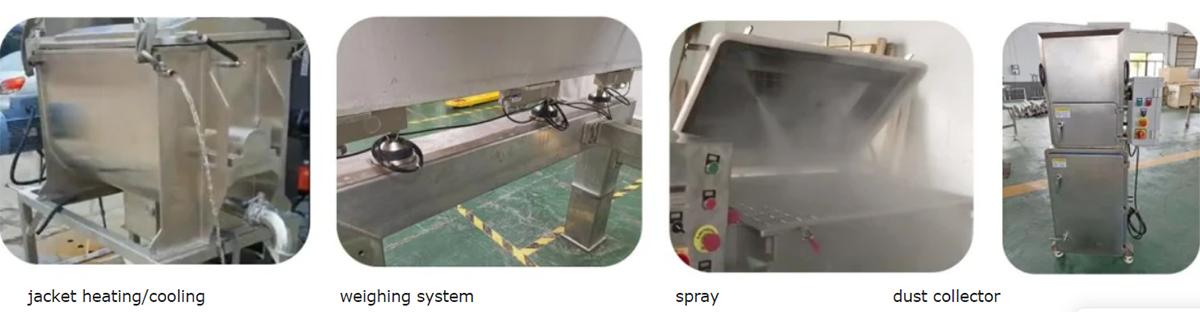
Auxiliary components such as a weighing system, a dust collection system, a spray system, and a jacket system for heating and cooling are commonly installed on mixers.
Post time: Apr-03-2024